news
お知らせ
【MONOist掲載!ものづくり太郎のPLM講座第一弾!】PLMこそ日本の製造業に必要な理由――プロセスをコントロールしろ!
ITmedia
2025, 5, 14
.png&w=828&q=75)
MONOistに連載が決定!
連載初回となる今回は、PLMの必要性を解説します!
日本の製造業は、「すり合わせ」や「現場力」に強みを持つ一方で、
設計、製造、調達といった部門間で情報が分断され、手作業による煩雑な調整業務が常態化しています。
第一回目となる今回は、このような現状を変革すべき理由と、PLMの基礎知識を掘り下げます。
ーーーーーーーーーーーーーーーーーーーー記事ーーーーーーーーーーーーーーーーーーーー
複雑性が強みとなっている日本の製造業
日本の製造業でITシステムの導入といえば、まずERP(Enterprise Resource Planning、企業資源計画)システムが想像される。ERPシステムとは販売、生産、購買管理などを連携し、期間損益の管理ができる会計システムだ。ERPシステムの導入には数億~1000億円規模での投資が必要とされる。上場企業であれば決算報告を行うために、ERPシステムを導入している企業が多いだろう。
ただ、ERPシステムで取り扱う情報は「コトの結末」となる事後情報だ。事後処理情報の管理システムである会計ソフトに投資する日本だが、本来の日本の製造業の強さはプロセスにこそある。俗に言う「すり合わせ」というものだ。もちろん事後処理である会計ソフトに投資することも必要なことだが、われわれが強みとする「すり合わせ」を強める投資はどちらかというと後回しにされてきた。
下図を見てほしい。これはハーバード大学グロースラボが発表している経済複雑性指標(ECI:Economic Complexity Index)を国別で並べたランキングだが、日本は2位であり、世界的に見ても産業が複雑性を持った構造となっていることが分かる。ハーバード大学の定義によると、ECIは、輸出構成の多様性や複雑性に基づいて算出されており、複雑で専門的な生産ノウハウを多様に持つ国が、洗練された多彩な製品の生産が可能であるため、複雑性がその国の所得水準予測を超える場合、その国は高い成長を遂げると予測している。つまり、日本は複雑で多様な生産システムを抱えているということが、高い成長ポテンシャルとなっていることが示されているのだ。
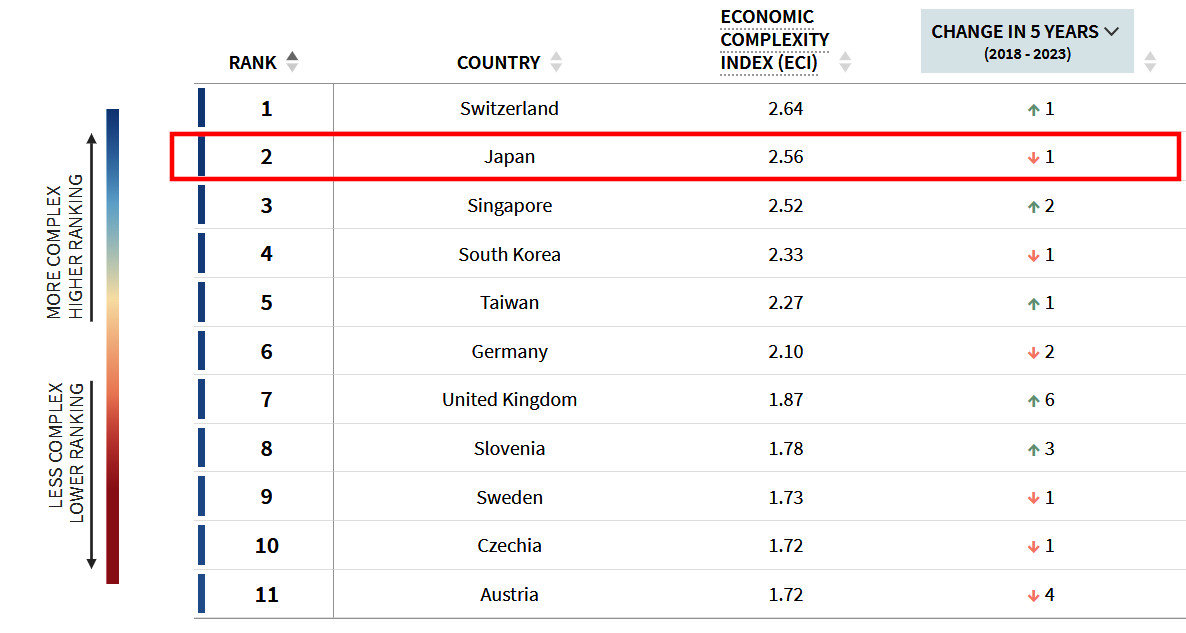
経済複雑性ランキング 出所:ハーバード大学グロースラボ「経済複雑性ランキング」
同様に経済複雑性指標から日本の産業を見ていくと、規模が大きいのが自動車だ。これは複雑性という意味で想像しやすいのではないだろうか。現在はEV(電気自動車)も自動車のラインアップの一部になっているため明言することはできないが、自動車は約3万点の部品から構成されているといわれている。トヨタ自動車や日産自動車は、7割(約2万点以上)の部品やモジュールをサプライヤーから購入しており、3割の部品のみを自社で製造しているのが現状だ。
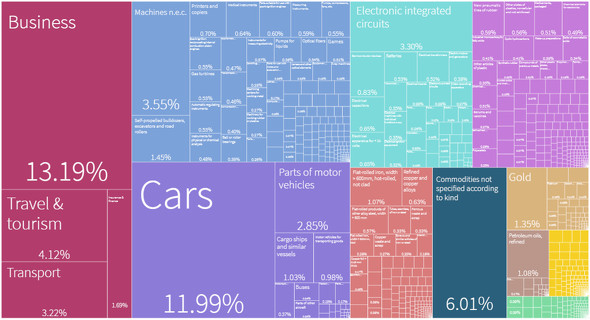
日本の産業分布出所:ハーバード大学グロースラボ「経済複雑性ランキング」
外作されるモジュールの1点ずつが、設計、開発、検証を繰り返して製造ラインに流れる。サプライヤーで部品やモジュールが製造され、品質を担保された後にOEM(自動車メーカー)に供給される。クルマはこうした数万点の部品を組み合わせて製造される。部品やモジュール、最終製品、それぞれで先ほどのプロセスが発生することをイメージすると、製品を製造するためには膨大な「すり合わせ」が発生していることが分かるだろう。
これは産業によっても異なる。例えば、ツーリズムをイメージするとどうだろうか。バングラディッシュやタイと日本のホテルを比較すると、地域性やサービス内容などで違いはあるものの、オペレーションやシステムに大きな差はないだろう。自動車と比較するとそこまで複雑性はないといえるのではないだろうか。つまり、日本の産業の強みは複雑な「すり合わせ」が多いモノづくり領域でこそ、成長のポテンシャルを発揮し、世界に冠たる経済大国になったといえる。30年以上前には「Japan as No.1」として米国で日本脅威論も持ち上がったこともあった。
半導体製造装置や自動車など、モノづくりに関わる企業を数多く見た経験から述べると、この強みについて日本企業は本当の意味を理解できているのかという危機感がある。その最たる例が、ITシステムへの投資配分だ。冒頭に述べた通り、ERPシステムは会計システムであり、事後情報の管理には役立つが、日本が強みとしてきた「複雑なすり合わせ領域をコントロールする」事前情報の管理や予測にはそれほど貢献しない。では、それに代わるシステムへの投資が進んでいるのかというと、全く投資していない企業も多い。日本の強みであるプロセスをコントロールする術を手に入れるべきではないだろうか。筆者はそれがPLM(Product Lifecycle Management)システムだと考えている。
少し具体的に話そう。例えば、自動車業界のTier1サプライヤー企業をイメージしてみよう。Tier1企業では、売上高2000億~数兆円規模で、保有する製造ラインの数は、全世界で300~5000ラインにも上る。経営者であれば、各ラインで製造しているワークの原価や売上高など、把握しなければならない項目は多岐にわたる。「ワークの製造方法が適切であったのか」「QC(品質管理)はどのレベルだったのか」など、現場のプロセスの情報を知りたいはずだ。
しかし、日本の多くの企業は、ラインごとの情報を経営情報に引き付けた形でほとんど持つことができていない。つまり「どのラインがもうかっているのか」「どのラインの生産効率が良いのか」「どのラインで製造された製品の品質が良かったのか」などの情報を持ち合わせていないケースがほとんどだ。決算期になって初めて全体の原価や利益が分かる程度である。にもかかわらず、経営の意思決定をしなければならない。
そもそもどのラインで製造されたモデルがもうかっているかは製造しないと分からず、製造しても詳細の把握ができていない。例えば、一般的にOEM(自動車メーカー)へモジュールを供給するためには見積もりの作成が必要だが、過去に製造したモジュールのプロセス情報や過去トラ(過去トラブル)などが不明確(データとして残っていない、コントロールできていない)ため、仕様要件にあった見積もりを作成することでさえ、一から作り上げるケースが多い。例えば、日本企業の中には見積もりの算出に約半年もかかっている場合もあると聞く。令和の時代に見積もり算出に6カ月もかかる状態で、果たして今後グローバル競争で戦っていけるのだろうか。
なぜ日本の製造業ではPLMが普及していないのか
ではなぜ、原価を集約させる機能やプロセスをコントロールする術を持っていないのだろうか。理由は「2次元図面」にある。日本の製造現場ではコントロールの中心が2次元図面となっており、それが多用されている。トヨタグループでさえ、現場に行けば2次元図面が貼り出されており、2次元図面で現場のコントロールをしている。Tier1企業を訪問すれば、ご丁寧にトヨタ専用見学ラインなるものが用意されており、全ての工程ごとに紙図面(2次元図面)が張り出されている。
決して勘違いしていただきたくないのは、2次元図面が悪いと言いたいのではない。重要なのは、2次元図面のみで現場をコントロールするとプロセスの情報が上流とひも付かないということだ。
もう少し細かく説明する。現在さまざまな設計は3D CADで行われており、最初はさまざまな設計データは3次元で作られている。では、現場での2次元図面はどのように生成されるかというと、3次元図面(3D CADモデル)から、2次元図面を人力で転写して生成しているのだ。例えば、あるメガサプライヤーでは、本社に150人以上のパートタイム人材を出社させ、3次元図面からタイピング(人力)で2次元図面をわざわざ作成している。
スマホ世代の若者がこの現状を聞くと全く非効率極まりないと考えるだろう。なぜここまでして2次元図面が必要なのだろうか。
それは2次元図面が現場の「コミュニケーションツール」だからである。例えば、ネジを製作するにしても、材料を投入する工程から、複数の加工を経て最後にバリ取りする工程までの情報を2次元図面に記載する。加工対象物の位置決め方法や、必要な人工(にんく)の情報、NCパス、装置の情報などさまざまな現場(プロセス)情報を2次元図面に集約して現場をコントロールしていく。仕様変更があれば注記を行うなどディビジョンの管理をし、2次元図面を都度改定しているのだ。この様に2次元図面は現場でなくてはならないものであり、2次元図面ですり合わせ(プロセスのコントロール)を行っている。
要するに2次元図面によるすり合わせ力(プロセスのコントロール力)で日本はJapan as No.1と呼ばれるように世界を制覇したのだ。当時はデジタルツールなどがない中で紙ベースのオペレーションで高品質な製品を高効率に作り出すためには、こうしたやり方が非常に優れていた。
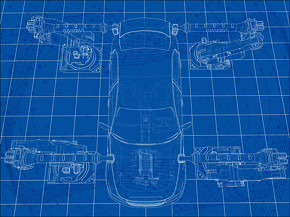
(※)写真はイメージです
一方で、Japan as No.1と呼ばれてから久しく、2次元図面のみで現場を運用する方法には限界が来ている。問題点として大きなものが、開発設計者と製造現場の断絶を引き起こしていることだ。3次元図面(3D CAD)を生成する際に出力される部品表(BOM: Bill of Materials)に現場(プロセス)情報がひも付かない。そのため、BOM(必要なモジュールや部品などを一覧表にしたもの)を中心として原価の情報や現場のコストの情報などひも付ける仕組みがなく、データとしても保管される仕組みが無いため、設計者や開発者、調達担当者にプロセス情報が伝わらない。
そのため実際に製造を行った結果、「原価やQCの情報、製造方法が正しかったのか」それとも「製造が難しく、品質を安定させるために多くの工数が必要だったのか」「改善によってスループットを最適化でき、原価がどの程度下がったのか」などの情報が全く活用されないままになっている。つまり、蓋を開けるとそうなっていたという事後の情報しかなく「決算時になんとなくもうかっている」という情報しか残らないわけだ。
現場での努力が設計者や調達担当者に伝わらないと言い換えてもいいかもしれない。OEM(自動車メーカー)が定期的に価格低減圧力を行使するのは、つまるところモジュールや部品ごとのもうけなどが分かっていない証拠だともいえる。モジュールごとにもうけや製造の難易度が判断できれば、その都度交渉できるが、OEMから仕事を受けるサプライヤーはプロセス情報を管理できていないため、毎年曖昧(あいまい)な値引き交渉を強いられているのである。
なぜ日本の製造業にPLMが必要なのか
今の日本は事後処理の会計システムを中心にオペレーションが回っており、四半期ベースごとの曖昧な情報しか分からず、製品の製造にかかったコストや必要な装置数、つくりやすさなどの情報が分からない。厳密には、設計者が利用しているCADやPDMのシステムは保有しているが、調達や生産準備、生産技術が利用するシステム(M-BOMやBOP)との連携が取れていない状況だ。
日本人は「すり合わせ」という各部門での膨大な人依存による連携で支えてきたが、現在は各部門を連携し、可視化できるシステムやソリューションが多く登場している。さらにAI(人工知能)が加わり、海外では日本の現場とはかけ離れた運用方法が始まりつつある。設計と製造現場、設計と調達、設計とメンテナンスサービス、調達とメンテナンスサービス、設計と営業など、さまざまな業務を連携させ情報をコントロールする時代に突入したと言っていい。
情報のコントロールにはBOMを中心としたデータ管理が必須であり、BOM情報を基にプロセス(QCD)をコントロールすることが必要になる。すなわちPLMの世界こそが日本に必要だ。もちろんPLMの運用にはERPとの連携も重要な要素になってくる。ただ、日本ではERPの投資ばかりが議論の中心になっているが、製造業にとってはPLMも同等以上に大切なはずだ。日本の強みであるプロセスをコントロールするPLMの重要性にフォーカスを当ててみてもいいのではないだろうか。
今後は、世界の動態を含め、最新のBOM管理やPLMのソリューションを毎月共有していく。連載を楽しみにしていてほしい。
ーーーーーーーーーーーーーーーーーーーーーーーーーーーーーーーーーーーーーーーーーー
記事はコチラ↓
https://monoist.itmedia.co.jp/mn/articles/2505/14/news001.html
現在、第二回目を作成中…
乞うご期待ください!